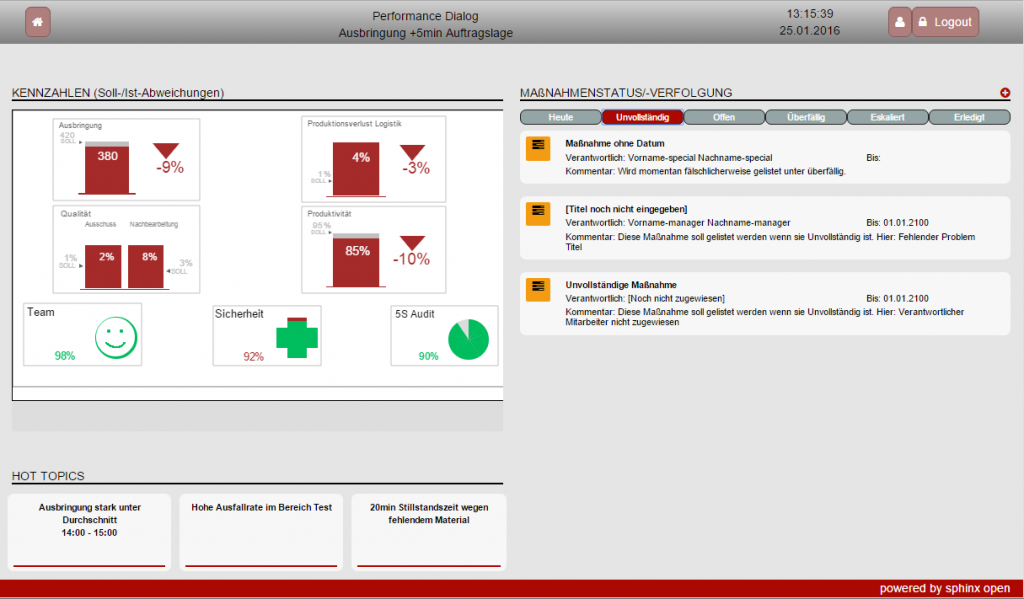
Die Digitalisierung macht vieles transparenter: Die Vorlieben von Konsumenten. Die Vorgeschichten von Patienten. Die Verbrauchsdaten von Gebäuden. Die Lagerbestände von Logistikunternehmen. Doch die damit einher gehende Flut von Daten kann anstrengend sein. Sie bietet aber bei sinnvollem Umgang zahlreiche Möglichkeiten, um den Alltag einfacher zu gestalten, Zusammenhänge zu erkennen sowie Zeit und Geld zu sparen. Entscheidend ist dabei stets, sinnvolle Verknüpfungen zu erstellen und die Daten zielgruppengerecht aufzubereiten.
Digitale Einblicke und Eingriffsmöglichkeiten
Eine bedeutende Zielgruppe im Rahmen der Digitalisierung der Industrie sind die Produktionsverantwortlichen – sowohl die Planer als auch die Werker. Deshalb ist Transparenz auf dem Shopfloor so wichtig. Und zwar in dreierlei Hinsicht: In einer modernen Fabrik sollte es möglich sein digitale Einblicke und Eingriffsmöglichkeiten zu erhalten bei a) den Aufträgen, b) dem Status der Maschinen und Anlagen, c) der Verfügbarkeit von Produktions- und Verbrauchsmaterial – und zwar in Echtzeit und ortsunabhängig. Da diese Fülle an Anforderungen komplex und mit einem einzigen Softwareprodukt kaum lösbar ist, bietet sich der Einsatz von IoT-Plattformen an. Sie empfangen und verknüpfen Daten aus verschiedenen Systemen, werten sie aus, informieren, visualisieren und antizipieren. Legt man definierte Regelwerke oder gar künstliche Intelligenz zugrunde, lassen sich die angeschlossenen Umgebungen über die Plattform automatisch steuern. Auf diese Weise können Firmen die Shopfloor-Transparenz deutlich erhöhen, vorhandene Ressourcen effizienter nutzen, präventive Maßnahmen durchführen und wichtige Prozesse optimieren. Typische Beispiele sind Trackingsysteme bei Logistikunternehmen, automatisierte Fehlermeldungen aus dem Maschinenpark oder vollautomatisierte Produktionsabläufe.
Modulare IoT-Plattformen
Besonders flexibel sind modulare IoT-Plattformen, die auf offenen Standards basieren, z.B. Sphinx Open Online der Firma In-Integrierte Informationssysteme, einem Tochterunternehmen von GFT Technologies. Diese Plattformlösung erschließt nicht nur diverse Datenquellen, sondern verknüpft die Daten intelligent, analysiert sie und bereitet sie rollenspezifisch für den Anwender auf. Über verschiedene Services lassen sich Informationen an jedem gewünschten Ort visualisieren und stehen so im Shopfloor, im Leitstand oder auf mobilen Devices zur Verfügung. Sphinx Open Online bringt dabei die Besonderheit mit, dass alle Aufgaben wie Datenanbindung, Auswertung, Überwachung und Prognosen in einem zentralen Modell, dem sogenannten Model in the Middle, koordiniert werden. Bei diesem Ansatz sind digitale Abbilder (Digital Twins) von Anlagen, Systemen und Prozessen bidirektional miteinander vernetzt. Für die dabei entstehenden Datenmengen bietet sich ein Betrieb in der Cloud an, wobei Sphinx Open Online auf allen maßgeblichen Cloudplattformen läuft – aber natürlich auch im Edge-Betrieb eingesetzt werden kann.
Visuelles Abbild der Produktion
Ein Service im Rahmen der IoT-Plattform ist das digitale Teamboard, das die Produktion visuell abbildet und eine effiziente Kommunikation im Produktionsteam ermöglicht. Sind die vorhandenen Datenquellen einmal angebunden, ergibt sich eine stets aktuelle grafische Darstellung des kompletten Produktionsbereichs mit Echtzeit-Daten. Diese Shopfloor-Transparenz ist in vielerlei Hinsicht nützlich: Für die täglichen Produktionsbesprechungen lassen sich Chart-Darstellungen von Produktions- und Qualitätskennzahlen aufrufen. Auch Probleme und Störungen sind leicht erkennbar. Der Produktionsverantwortliche kann sich bei Bedarf alarmieren lassen, wenn Abweichungen vom Standardprozess auftreten. Für die gemeinsame Analyse der Vorkommnisse bietet das Teamboard die Möglichkeit, Problemursachen und deren Abhängigkeiten abzubilden. So ist es ein Leichtes, Verbesserungsmaßnahmen zu definieren und deren Wirksamkeit zu überprüfen. Das ist bereits eine relativ ausgeklügelte Ausbaustufe. Viele produzierende Unternehmen sind im Moment von dieser digitalen Art der Shopfloor-Organisation noch ein gutes Stück weit entfernt. Umso größer ist der Hebel, wenn sie die ersten Schritte Richtung Digitalisierung gehen. Allein die Transparenz über den Gerätestatus, also darüber, welche Maschine wie häufig produziert bzw. stillsteht, ist oft ein großer Mehrwert. Bauchgefühle und Mutmaßungen gehören damit der Vergangenheit an und werden abgelöst von eindeutigen Zahlen. Die Erkenntnisse zu Auslastung oder Nicht-Auslastung sind anfangs oft überraschend und legen Problempunkte offen. In der Folge können gezielte Maßnahmen ergriffen werden. Datentransparenz ist also immer der erste Schritt und die Basis für Verbesserungen.
Verringerte Durchlaufzeiten
Aktuelle Projekte der GFT-Gruppe haben gezeigt, dass die Einführung eines Tools zur digitalen Visualisierung und Verbesserung der Shopfloor-Aktivitäten die Durchlaufzeiten erheblich verringert. Werte von 40 Prozent und mehr sind hier keine Seltenheit. Auch die Liefertreue steigt in der Regel schnell an. Positiv für den Gesamtprozess ist auch, dass dank der höheren Transparenz die Anzahl der Lagerteile und halbfertigen Komponenten, die auf Weiterbearbeitung warten, spürbar reduziert werden kann. Es gibt Kunden, die nur noch halb so viele Teile zur Seite legen müssen, so dass die Mitarbeiter den Platz in der Fertigung und im Lager effizienter nutzen können. Mit den zahlenmäßigen Erfolgen steigen in der Regel auch Kunden- und Mitarbeiterzufriedenheit.
Beispiel aus der Blechbearbeitung
Ein aktuelles Beispiel für eine geglückte Optimierung im Produktionsbereich liefert das Blechbearbeitungsunternehmen HA-BE Gehäusebau mit der Neueinführung einer Pulverbeschichtungsanlage. Seit die Maschine über OPC UA an die firmeneigenen IT-Systeme angebunden ist, sorgt Sphinx Open Online für den Datenaustausch zwischen den beteiligten Menschen, Systemen und Anlagen. Über einen Barcodescanner werden eingehende Teile am Warenträger identifiziert. Das ERP-System holt sich automatisch die Datensätze zum Produktionsauftrag sowie Parameter für die Fertigung, dann wird der Parametersatz zur Steuerung der Pulverbeschichtungsanlage übertragen. Passend zu den jeweiligen Teilen wird dem Werker am Bildschirm grafisch angezeigt, welche vorbereitenden Schritte er auszuführen hat. Gibt er die Rückmeldenummer des Produktionsauftrags ein, erscheinen auf dem Monitor die relevanten Auftragsdaten aus dem ERP sowie die passenden Arbeitsanweisungen. Bei HA-BE kristallisieren sich auf Basis der IoT-Plattform inzwischen weitere Einsatzmöglichkeiten heraus. Das Unternehmen plant einen elektronischen Rüstplan für die Werker, der zusätzlich auch die Stanz- und Biegemaschinen beinhaltet. Außerdem ist ein Shopfloor-Management zur Optimierung der Maschinenauslastung angedacht. Ein weiterer Ansatz besteht in der Energiekostenoptimierung durch den intelligent geregelten Einsatz des Blockheizkraftwerks für Strom- und Wärmeerzeugung. Und das ist sicherlich erst der Anfang. Derart vielgestaltige und komplexe Anforderungen werden in Zukunft nur mit Hilfe einer leistungsfähigen IoT-Plattform wirtschaftlich in die Tat umsetzbar sein.