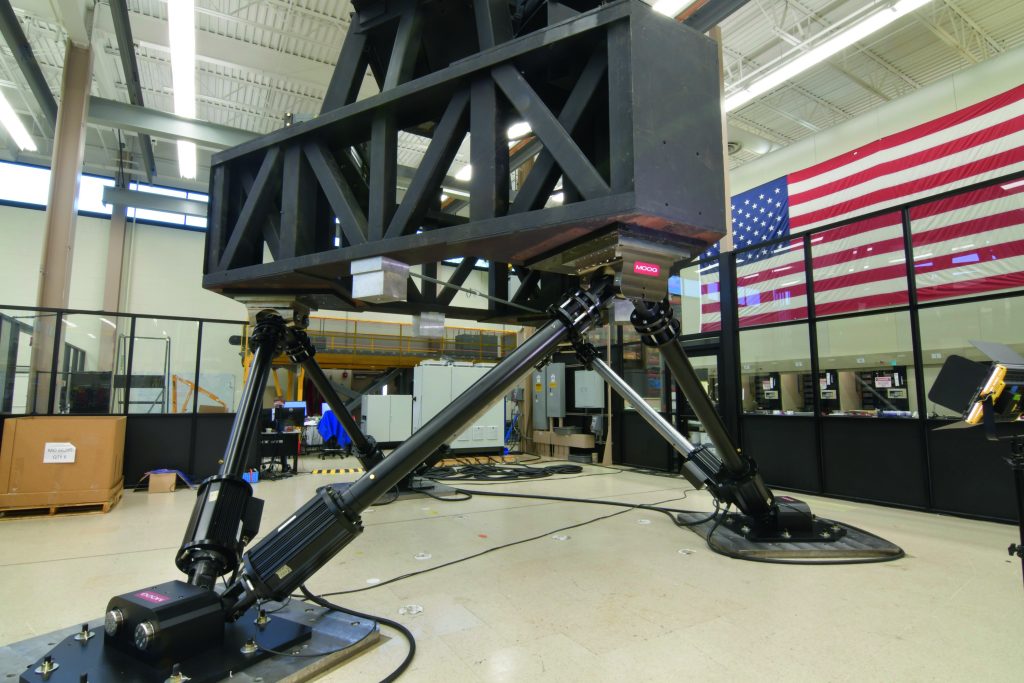
Simulationsplattformen von Moog werden in der Pilotenausbildung für die Luft- und Raumfahrt eingesetzt. Auch bei der Alltags-Tauglichkeitsprüfung im Motorsport und in der Fahrzeugentwicklung ist man auf diese Lösungen angewiesen. Mit einer installierten Basis von über 1.000 Simulator-Bewegungssystemen weltweit, hat der Antriebsanbieter in diesem Bereich jede Menge Erfahrung und kennt alle Stellschrauben, an denen man für mehr Effizienz drehen kann. So ist es Moog bei der neuen Baureihe Gen3 gelungen, den Energieverbrauch um 65 Prozent auf 20 bis 25kVA zu senken – ohne Einbußen bei der Bewegungsqualität.
Möglich wurde dieses Ergebnis durch den Einsatz der smarten DE2020-Antriebsregelung und einer damit verbundenen, neuen Herangehensweise. Vormals wurde Energieversorgung immer auf die Spitzenlasten eines Antriebssystems ausgelegt, selbst wenn diese Höchstwerte nur selten vorkommen. Dieses energetische Vorhalten ist aber mit erheblichen elektrischen Verlusten und auch mit Kosten hinsichtlich Kabelauslegung und Anschlussleistungen beim Versorger verbunden.
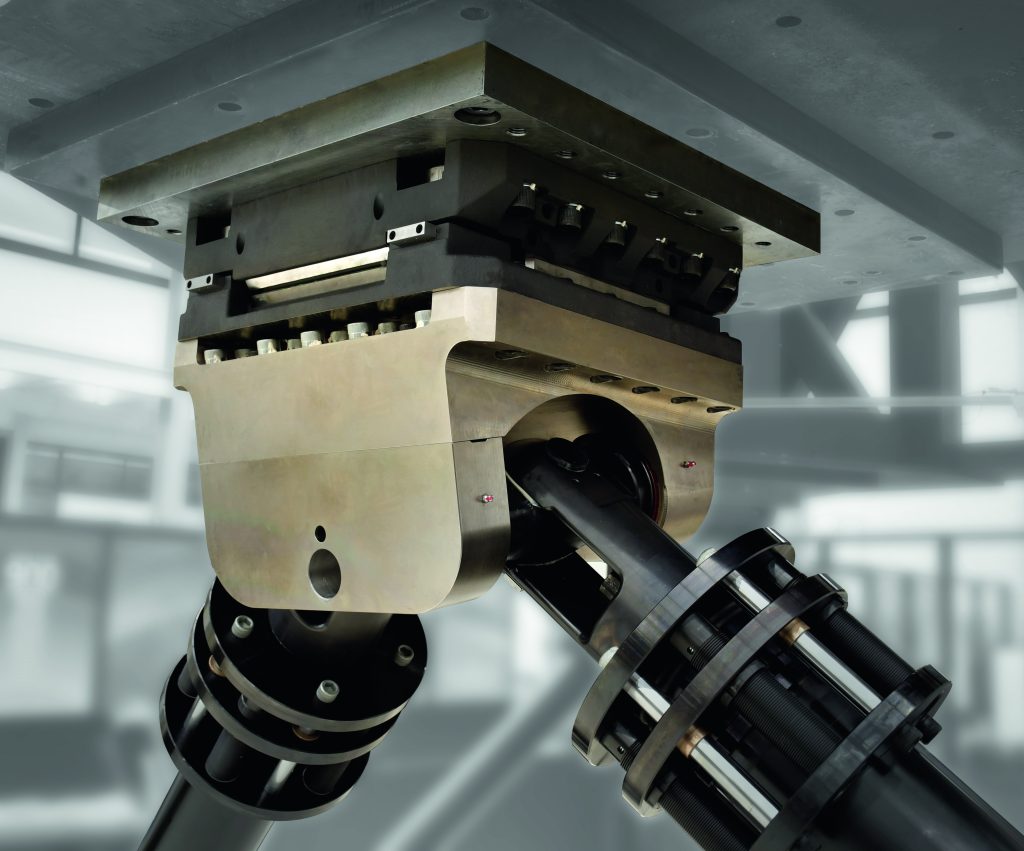
Elektrischer Leistungsschub
Könnte man nicht kurzfristige Lasten innerhalb des Systems abfedern und es eventuell aus Leistungsüberschüssen aufladen? Ähnlich dem elektrischen Leistungsschub der Formel 1? Diese Fragestellung hat Eingang in die Entwicklung eines Energiemanagement-Systems für die DE2020-Antriebsregelung gefunden. Klar ist, der Normallauf eines Motors oder Bewegungssystems verursacht die Regellast, bei Beschleunigungsvorgängen wird kurzfristig mehr Energie benötigt, während die Freisetzung von Energie aus der mechanischen Beharrung oder beim Bremsen bislang zumeist ungenutzt in Wärme umgesetzt wird.
Das macht die neue Lösung nun anders: Während der Regellastphase wird eine Kondensatorbank sanft vorgeladen und noch offene Restkapazität vorgehalten. Lastspitzen deckt die DE2020-Antriebsregelung dann mit einem Leistungsabruf aus der Kondensatorbank ab, Energiegewinne aus Bremsen und mechanischer Beharrung nutzt er durch Rekuperation hingegen zum Aufladen der Kondensatoren. Diese sind damit für die nächste Lastspitze gerüstet. So können die Anschlusswerte beim Simulator-Bewegungssystem weitaus kleiner und nahe an der Regellast ausgelegt werden. Dieser Ansatz kann im Grunde auf alle elektrischen Antriebe übertragen werden. Darüber hinaus kann dieses System mittels Vorfilter und in Kombination mit der Kondensatorbank Netzschwankungen ausgleichen bzw. bei Netzausfall das System solange noch mit Energie versorgen, bis eine Sicherheitsposition angefahren ist. Die neue Moog-Lösung gibt die exakt benötigte Leistung im genau richtigen Moment ab. Positiver Nebeneffekt der gesamten Überarbeitung ist die kompakte Bauform des Schaltschrankes, der nur noch halb so groß ist wie beim Vorgänger und ein verminderter Bedarf an Kabelquerschnitten, um die Ströme fließen zu lassen.
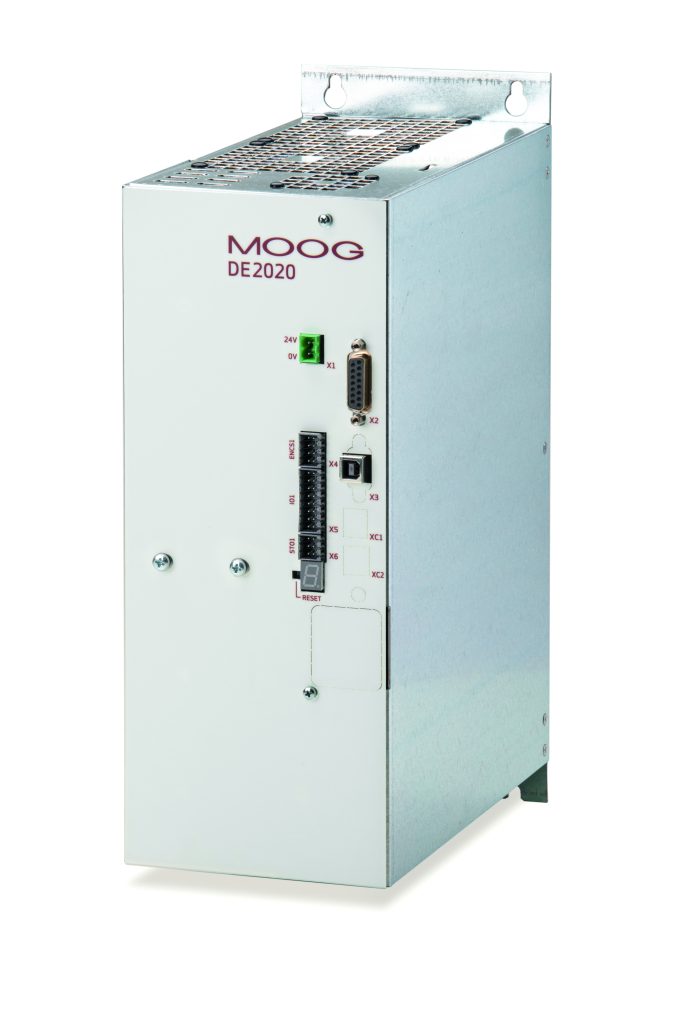
Flexibler, kompakter, sparsamer
Im Schaltschrank befindet sich zur Aktuatorensteuerung auch der DM2020-Servoantrieb. Er wurde auf die Ansteuerung und Versorgung mehrerer Achsen ausgelegt, sorgt mittels leistungsstarker Steuerplatine samt Software für hohe Geschwindigkeiten bzw. schnellere Zykluszeiten und kann verschiedene Motor- und Aktuatorentypen ansprechen. Eine hohe Synchronisation zwischen den Achsen wird durch die Implementierung des doppelachsigen Layouts in einem einzigen Modul und der Verbindung zwischen den Modulen über CANopen erreicht. Zusammen mit dem dazugehörigen Energiemanagement-System und einer gemeinsamen DC-Bus-Konfiguration wird ein direkter Energieaustausch zwischen den Achsen realisiert. Das kann den Energieverbrauch zusätzlich senken. Erst nach unmittelbarer Energieumleitung zwischen den Achsen wird auf die Reserve der der Antriebsregel-Einheit zugegriffen oder Überschuss in die Reserve eingestellt.
Das Gen3-Motion-System nutzt neue und schnelle Planetenrollengewindetriebe. Das bringt den generellen Vorteil, dass die Lösung trotz ihrer Kompaktheit hohe Lasten tragen und präzise beschleunigen bzw. bremsen kann. Hinsichtlich der Aktuatoren wurde für diesen Einsatz nochmals jedes Bauteil neu betrachtet. Im Ergebnis bestehen die Gen3-Aktuatoren nun aus weniger Einzelteilen und können, speziell was Verschleißteile angeht, vor Ort instand gesetzt werden. Das kann z.B. bei Dämpfungselementen sogar im laufenden Betrieb ohne Stopp und Ausbau des Aktuators geschehen. Gleiches gilt für Steckverbinder und Encoder-Baugruppen. Mit der Entwicklung der Gen3-Lösung ist es Moog gelungen, ungeplante Wartungsstopps um rund 22 Prozent zu reduzieren.
Hohe Ansprüche an die Antriebe
Wie bereits erwähnt: Von den Aktuatoren wird ein Gesamtgewicht von rund 14t je nach Typus um 1,07 bis 1,59m verlagert, um ca. 18 bis 32° je nach Achse gekippt und mit ca. 70cm pro Sekunde verfahren. Dabei laufen diese Bewegungen nicht iterativ sondern in Kopplung miteinander. Das stellt hohe Ansprüche an die Antriebstechnik. Von den Vorteilen der neuen Antriebsgeneration sollen auch weitere Bereiche wie industrielle Automatisierung, Prüfstände, Handhabung oder Robotik profitieren.