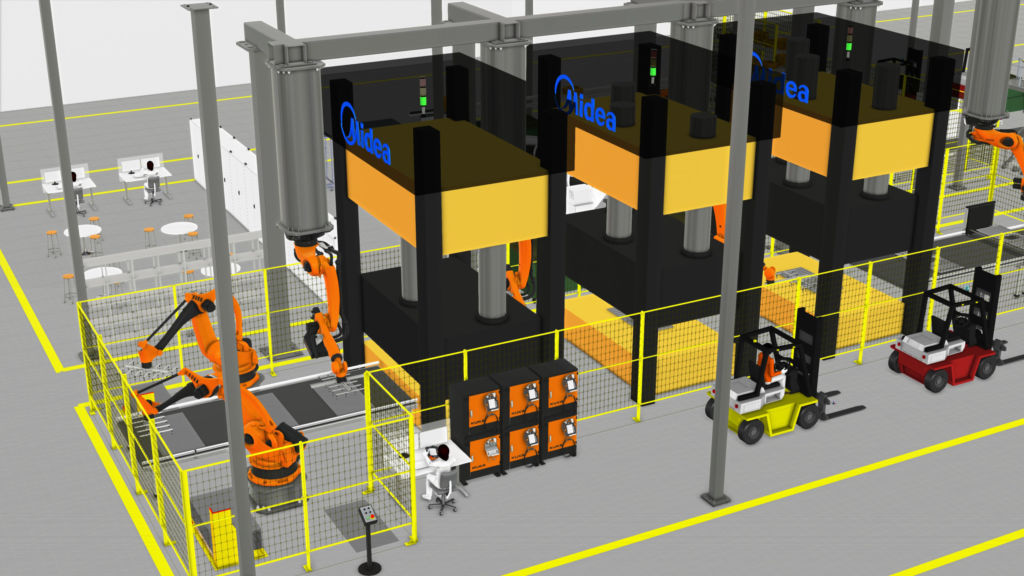
Die Midea Group wurde 1968 gegründet und hat ihren Hauptsitz in Südchina und bezeichnet sich selbst als größten Hersteller von Haushaltsgroßgeräten und führende Marke bei Luftaufbereitungssystemen, Klimaanlagen, Kesseln und Reiskochern. Die Abteilung für Waschmaschinen umfasst auch ein Digital Center mit einem Team von Simulationsingenieuren, die dafür verantwortlich sind, die Gestaltung des Produkts, der Werkzeuge und der Anlagen zu prüfen ebenso wie die Robotertechnik, die Logistik und das Fabriklayout.
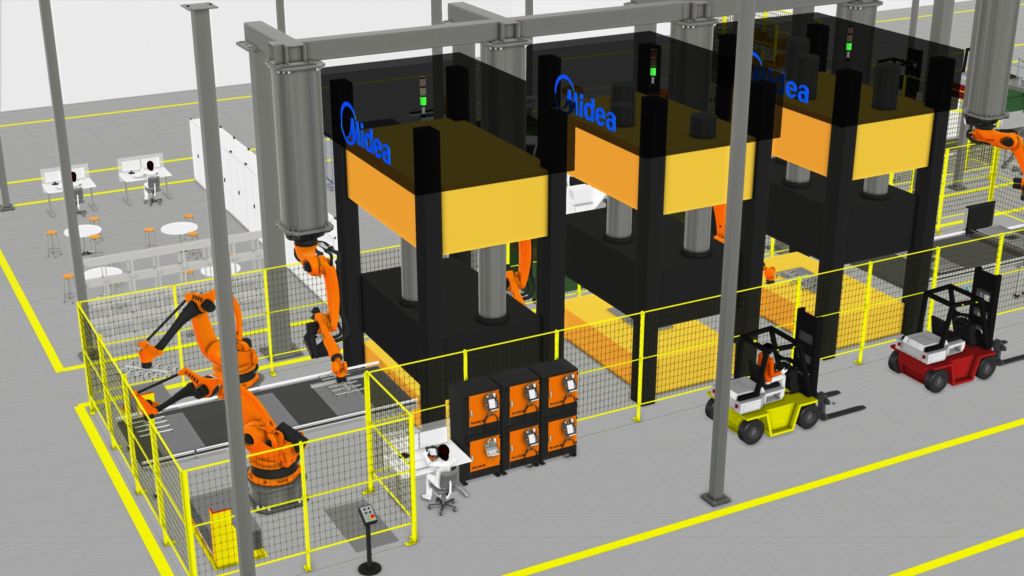
Neue Montagelinie in China
2018 begann Midea ein Projekt zur Einführung einer flexiblen Montagelinie für die Herstellung von Highend-Waschmaschinen. Die neue Montagelinie sollte im Werk von Wuxi, China, in der Abteilung für Waschmaschinen gebaut werden. Neben der Herstellung von hochwertigen Highend-Waschmaschinen wollte Midea, dass auf dieser Linie auch Aufträge für personalisierte und kundenspezifische Waschmaschinen hergestellt werden konnten. Das Simulationsteam war verantwortlich für die Prüfung des Entwurfs und des Layouts der Montagelinie und sollte das Feedback liefern, wie man sie verbessern könnte.
Obwohl die Bruttogewinnmarge für diese Highend-Waschmaschinen höher war als bei den bereits von Midea gefertigten Waschmaschinen, so waren die Produktionsanforderungen auch höher. Es gab größere Anforderungen an die technische Kontrolle in Bezug auf Materialien, Prozesse und fertige Produkte. Aufgrund der komplexen Herstellung und der Anforderungen an die Zeitplanung musste die Montagelinie verstärkt auf intelligente Fertigungsfähigkeiten zurückgreifen und eine flexible Produktionskapazität bereitstellen.
Einzigartig an diesem Projekt war auch, dass die Montagelinie die Kapazität benötigte, um mehr als zehn verschiedene Produktplattformen und über 100 Artikelpositionen zur selben Zeit herzustellen – die alle durcheinandergemischt sind und alle ihre eigenen, spezifischen Verarbeitungszeiten, Materialanforderungen und Qualitätskontrollverfahren haben. Dafür mussten mehr als 100 Arbeitsvorgänge neu angepasst werden, die sich von den bisher verwendeten Mustern für Serienfertigung grundlegend unterschieden.
Schnelle und einfache Modellierung von Anlagen und Prozessen
„Als Simulationswerkzeug spielte Visual Components eine wichtige Rolle bei diesem Projekt“, sagt Fanshi Kong, Ph.D, Simulationsingenieur des Digital Center-Teams. „Vorher verwendeten wir drei unterschiedliche Produkte, um 3D-Layouts zu gestalten und Ausrüstung, Logistik und Produktionskapazität zu prüfen.“ Das Produkt, das Fanshi Kong und sein Team bis dahin zur Schaffung von CAD-Modellen und 3D-Layouts verwendeten, war sehr schwerfällig, insbesondere wenn es darum ging, komplexe Maschinen oder Ausrüstung zu modellieren. Die umfangreiche Bibliothek von parametrischen und wiederverwendbaren Modellen des E-Katalogs von Visual Components vereinfachte Kong und seinem Team die Modellerstellung.
Eine weitere Herausforderung war die fehlende Kompatibilität zwischen ihrer CAD-Software und der Software für Anlagensimulation. Der Import von Modellen gestaltete sich schwierig. Nachdem es ihnen gelungen war, die Geometrie zu importieren, war es stets schwierig, die Bewegungen und das Verhalten der Modelle zu definieren. Ähnliche Erfahrungen machten sie mit dem Logistiksimulationswerkzeug: Auch hier überwogen komplexe Programmierung und zeitaufwendige Arbeit. Für das Team ist die Modellierung von Anlagen und Prozessen mit Visual Components viel schneller und einfacher. Besonders gefielen ihnen auch die Grafiken und die Videoausgabe. Schon nach einer kurzen Probezeit kam Visual Components als primäres Simulationswerkzeug des Teams von Kong zum Einsatz. „Als sich herausstellte, dass Visual Components viel mehr Vorteile im Vergleich zu diesen anderen Produkten bietet, sind wir schrittweise auf die Software umgestiegen, um die meisten unserer Projektfälle zu simulieren“, erklärt der Simulationsingenieur.
Kong und sein Team haben Visual Components verwendet, um den Prozess und die Durchführbarkeit des Layouts für das Waschmaschinenprojekt zu entwerfen, anzupassen und zu prüfen. Gleichzeitig konnten sie die geplante Montagelinie und das Logistiklayout dem Vorstand von Midea und den am Projekt beteiligten Stakeholdern dynamisch präsentieren.
Prüfung des Entwurfs und des Layouts der Montagelinie
Mehr als 100 Komponenten müssen montiert werden, um die Highend-Waschmaschinen zu fertigen. Das gesamte Projekt für die Montagelinie setzte sich aus drei Hauptmontagelinien zusammen:
- 1. Trommelmontage: Die Trommelmontage setzt sich aus dem Einsetzen einer inneren Trommel in eine hintere Trommel zusammen, die dann mit einer vorderen Trommel versiegelt wird.
- 2. Gehäusemontage: Eine Stahlplatte wird in ein Stahlgehäuse unter Verwendung einer horizontalen Stanzmaschine eingefügt. Zubehör wie flexible Schläuche und Kabel werden am Gehäuse eingebaut und bilden die Gehäusemontage.
- 3. Waschmaschinenmontage: Die Trommel- und Gehäusegruppen werden zusammen mit dem Ausgleichsgewicht, dem Bedienfeld, der Tür und der Abdeckplatte zusammengebaut, um das fertige Produkt zu bilden.
Für Kong und sein Team gab es für dieses Projekt zwei große Herausforderungen. Die erste bestand darin, Probleme während der Entwurfsphase zu erkennen und zu vermeiden, dass es während der Konstruktion und Implementierung zu Problemen kommt, deren Lösung deutlich teurer wäre. Darum war Simulation der Schlüssel zur Überwindung dieses Problems. „Wir haben unseren Entwurf mit Hilfe der Simulation überprüft“, sagt der Simulationsingenieur des Digital Center-Teams. „Wir haben gezielt nach Risiken im Entwurf gesucht und die Simulation angewendet, um deren Auswirkungen zu minimieren oder zu beseitigen.“
Die zweite Herausforderung bestand darin, die beste Lösung zu finden, um die strengen Anforderungen und Ziele des Projekts zu erfüllen. Das Team nutzte die Simulation intensiv, um den Entwurf anzupassen. So führten sie z.B. mehr als 100 Simulationsfälle durch, um für die Arbeiter den besten Arbeitseinsatz zu finden. „Die Methoden, mit denen wir diese Herausforderungen bewältigt haben, waren bisher unvorstellbar“, so der Simulationsingenieur. „Es war bisher nicht so einfach, eine Lösung zu entwickeln, ohne die Linie tatsächlich zu bauen und zu testen. Mit Visual Components können wir einfach alle Arten von Lösungen in einer virtuellen Umgebung entwerfen, simulieren und überprüfen.“
Projektziele übertroffen
Das Team von Kong konnte signifikante Verbesserungen und Einsparungen gegenüber dem ursprünglichen Entwurf erzielen, angefangen mit einer effizienteren Nutzung der Stellfläche. „Wir haben die Stellfläche für die Montagelinie um zehn Prozent reduziert und gleichzeitig die Produktionskapazität um zehn Prozent erhöht“, so Kong. „Die Linie hatte genug Kapazität, um pro Jahr 500.000 Einheiten zu produzieren.“ Die Montagelinie konnte eine Mixed-Flow-Produktion von mehr als 100 SKUs im Vergleich zu den normalen 5 bis 10 SKUs aufnehmen. Die Abtaktung war trotz des komplexeren Produktionsprozesses ausgeglichener. „Die Abtaktung verbesserte sich um 20 Prozent und erreichte mehr als 90 Prozent“, sagt Kong.
Dem Team gelang es auch durch eine effizientere Personaleinsatzplanung und -auslastung, wie z.B. in der Produktion, Logistik und Qualitätskontrolle, Kosteneinsparungen zu erzielen. „Wir konnten die Mitarbeiterzahl gegenüber dem ursprünglichen Plan um 45 Prozent reduzieren, ohne Einbußen bei Leistung oder Produktqualität“, stellt Kong fest. „Wir konnten die Produktqualität sogar verbessern und die Ausschussquote von 1.200 Fehlern pro Million auf 120 Mängel pro Million Fertigungseinheiten senken.“
Schließlich konnte die Konstruktion und die Installation der kompletten Montagelinie beschleunigt werden. „Wir haben die Bauzeit von 15 auf 12 Wochen reduziert und damit 20 Prozent in der Terminplanung eingespart“, erklärt Kong. Die für das Projekt realisierten Gesamtkosteneinsparungen betrugen etwa 879.000US$. „Durch den Einsatz von Visual Components konnten wir niedrigere Investitions- und Arbeitskosten sowie deutliche Effizienzsteigerungen erzielen. Dadurch konnten die Gesamtkosten des Projekts um ca. 15 Prozent gesenkt werden“, so der Simulationsingenieur des Digital Center-Teams.